The Value of Managing Milk Temperature
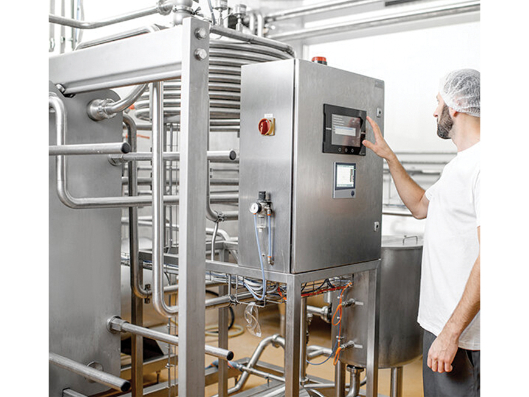
Article Courtesy of American Dairymen Staff
A dairy chiller is the most critical component in ensuring milk is made from cow to dairy counter at a safe and healthy temperature. So, how does the milking process work? Cow milking machines automatically pump milk from cows into refrigerated tanks. Once the milk is collected, the pasteurization process begins, and this is where a dairy chiller comes into play. The method of pasteurization heats milk. Dairy chillers remove heat during pasteurization and cool milk to an appropriate temperature. Keeping milk at a cool temperature prevents milk from growing harmful bacteria and deteriorating. Farmers can extend the milk’s storage life by using a dairy chiller and allowing time to transport milk to stores safely.According to the Dairy Practices Council, cooling milk immediately after milking keeps bacteria from multiplying rapidly. Holding milk at temperatures below 40°F (4°C) and above freezing maintains its excellent quality until it is processed for fluid milk or manufactured into dairy products. Each degree in temperature above 40°F(4°C) elevates bacteria counts and decreases the shelf life of finished products. Under PMO regulations, raw milk sold to processors must be less than 100,000 standard plate count. All farms have the capability of producing milk under 5000.
Close temperature control, clean milk, and sanitary equipment help many dairymen earn quality premiums and avoid penalties based on bacteria counts. Even though the regulatory limits are less stringent, reference PMO item 18r, ideal milk cooling systems on dairy farms should:
• Cool milk below 40°F (4°C) 30 minutes after the first milking ends,
• Hold the milk at 37-38°F (3°C), and
• Prevent temperatures from rising above 45°F(7°C) any time after four hours after the start of milking or during the addition of milk from subsequent milkings
This goal is more demanding than any state requirements of the national PMO (Pasteurized Milk Ordinance) recommendations. Still, meeting today’s standards for consistently producing high-quality milk is more appropriate.
Types of Dairy Chillers
The size of your dairy operation will decide what kind of dairy chiller you need. Older models of dairy chillers use a double-walled tank with water and cooling coils surrounding the milk tank. These older models of dairy chillers use a compressor, which builds ice around the coils in the double-walled area. Once the ice reaches a certain thickness, the compressor shuts off, and the ice quickly cools the milk. This older dairy chiller design works perfectly if you have a smaller dairy farm of up to 40 cows. Larger dairy farms require dairy chillers with a different type of design, such as a plate chiller. Plate chillers work well for large farms and are available in several styles. Most plate chillers use glycol and water to cool milk. These chillers push milk through stainless steel plates to a glycol and water mixture on the other side, which cools milk to an appropriate temperature.
Air-Cooled and Water-Cooled Chillers
Dairy chillers also come in air-cooled and water-cooled models. Air-cooled chillers transfer heat to the surrounding air, while water-cooled chillers transfer heat to a water source, such as a cooling tower. Water-cooled chillers require a mechanical room because they have special equipment that air-cooled chillers don’t have. Air-cooled chillers require an open, airy space because they rely on a consistent stream of fresh air. Water-cooled chillers are a bit more costly than air-cooled chillers but run on lower energy costs. Water-cooled chillers also require more maintenance than air-cooled ones because of the additional parts needed to run these machines. Air-cooled chillers are more accessible to set up than water-cooled chillers because they have a more simplistic design and perform best in areas that have water shortages.